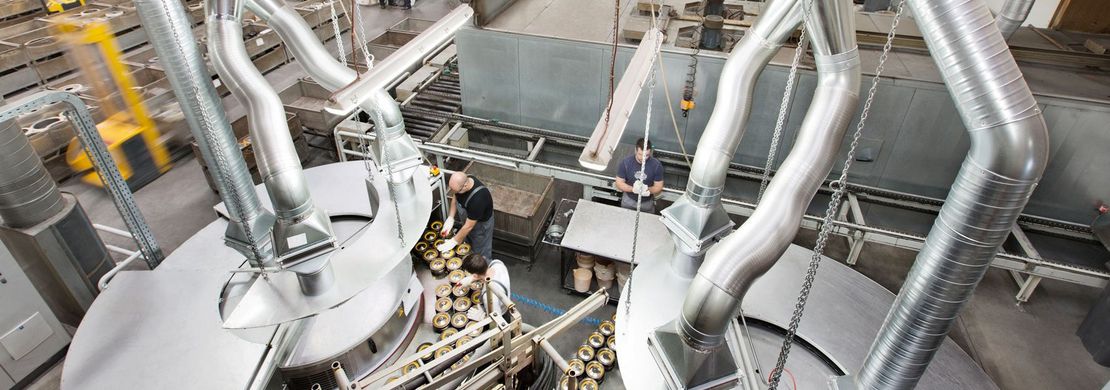
Gießen und Nachbehandlung
Unser Werk 2 wurde 2002 in Betrieb genommen und seitdem kontinuierlich weiter ausgebaut. Auf einer Fläche von 10.000 m2 produzieren wir hier täglich an der weltweit modernsten Produktionsanlage bis zu 12.000 Räder und Rollen mit VULKOLLAN® oder Polyurethan-Laufbelägen. Auch elektrisch leitfähige VULKOLLAN® ELF- sowie TRACTOTHAN® Räder werden hier nach patentierten Verfahren hergestellt.
Nach der mechanischen Bearbeitung in Werk 1 werden hier sämtliche Metallkerne gestrahlt, um eine metallisch reine Oberfläche zu erreichen, und dann in speziellen Waschmaschinen von Rückständen gereinigt, entfettet und vakuumgetrocknet. Anschließend folgt ein besonders sensibler Prozessschritt – der Bindemittelauftrag. In computergesteuerten Anlagen werden die Kerne mit einem speziellen Haftvermittler besprüht, der für die erforderliche Bindung zwischen Radkern und Belag sorgt.
Vor dem eigentlichen Beschichten werden unsere Radkörper dann in speziellen Einbrennöfen auf eine vorgeschriebene Gradzahl erhitzt, um Kern und Gießmaterial auf die gleiche Temperatur zu bringen und den Haftvermittler chemisch zu aktivieren. Im Maschinen- oder im Handguss werden die vorbereiteten Kerne dann mit den unterschiedlichsten Radbelagwerkstoffen, wie VULKOLLAN® oder PEVOPUR® beschichtet.
Bei der Herstellung von Polyurethan-Radbelägen im Heißgießverfahren laufen, unter streng kontrollierten Bedingungen, chemische Reaktionsprozesse ab, die erst lange nach dem Erhärten des Materials enden. Die Nachbehandlung der beschichteten Räder – das sogenannte Tempern – ist daher von größter Wichtigkeit und entscheidend für die exzellente Qualität unserer Produkte. In unserem Temperraum werden alle Produkte einer speziellen Prozedur nach vorgegebenen Parametern hinsichtlich Temperatur, Luftfeuchtigkeit und Temperdauer unterzogen.